L’histoire de Brandt a démarré en 1902, avec un atelier de serrurerie et ferronnerie. C’est seulement à partir de 1924 que la marque a lancé ses premiers appareils électroménagers. Elle saisit d’ailleurs l’occasion de cet anniversaire pour rappeler que durant ces cent ans, elle n’a cessé d’innover : on lui doit notamment les premiers fours à pyrolyse ou encore les tables de cuisson à induction. La célébration de ce centenaire sonne aussi un peu comme une revanche car Brandt a dû se battre pour préserver ses usines et continuer à produire dans l’Hexagone. C’est aujourd’hui le dernier industriel à concevoir et fabriquer du gros électroménager en France.
Usine Brandt d'Orléans : un site où savoir-faire et excellence s’appuient sur l’humain
Pour célébrer ses 100 ans, Brandt a convié la presse à visiter son usine de Saint-Jean-de-la-Ruelle, à côté d’Orléans. Spécialisé dans la production d’appareils de cuisson des marques Brandt, De Dietrich et Sauter, ce site emblématique du Groupe Brandt est un fleuron de l’industrie française et l’un des derniers bastions du gros électroménager made in France. Un choix pour lequel l'entreprise s’est battue et qui constitue aujourd’hui une valeur ajoutée.
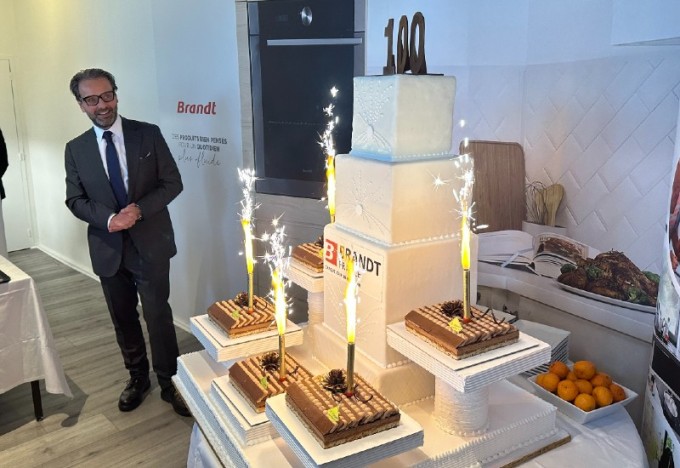
"Produire en France n’est pas un coût, c’est une valeur ajoutée"
Voilà l’une des phrases marquantes qu’a prononcées Daniele Degli Emili lors de son discours. En l’occurrence, le Groupe Brandt, qui compte 750 employés dans l’Hexagone, n’est pas seulement installé à Saint-Jean-de-la-Ruelle mais sur quatre sites au total. Celui que nous avons visité à côté d’Orléans est le plus important ; 350 personnes y travaillent. Il accueille l’une des usines ainsi que la R&D (qui compte 60 personnes). Le groupe dispose d’une seconde usine, à Vendôme, où travaillent 100 personnes. Le siège, qui compte 200 employés, est installé à Rueil-Malmaison. Pour finir, une centaine de personnes travaillent à Cergy, au SAV.
Daniele Degli Emili souligne la volonté de l'entreprise de rester implantée en France, pas seulement pour ses activités de production mais aussi pour le développement des produits et le service après-vente qui est intégré. « Produire en France est doublement important pour le groupe. Pour l’engagement social, puisque cela permet de maintenir des emplois en France, et également pour réduire l’empreinte carbone tant sur la fabrication que sur le transport de nos produits vers l’utilisateur » explique-t-il. En effet, grâce à la localisation des deux sites industriels en région Centre-Val de Loire, quel que soit le lieu où les produits sont expédiés en France, ils parcourent moins de 1000 km pour être livrés.
Enfin, le made in France revêt aussi une valeur ajoutée indubitable à l’export, notamment en Asie. D’ailleurs, le Groupe Brandt étend sans cesse ses activités à de nouveaux marchés – comme l’Australie et le Canada, par exemple, où il sera présent sous peu.
En outre, les produits de cuisson des marques De Dietrich, Brandt et Sauter ne sont pas seulement fabriqués en France ; ils bénéficient également de la certification Origine France Garantie. Gilles Attaf, président d’Origine France Garantie, était d’ailleurs présent lors de cette visite de l’usine ; il était accompagné d’Arnaud Montebourg.
Deux usines qui se répartissent la fabrication des appareils de cuisson
Le groupe compte donc deux usines dans l’Hexagone, où sont fabriqués une majorité des fours et tables de cuisson de ses marques De Dietrich, Brandt et Sauter. Celle de Saint-Jean-de-la-Ruelle (qu’on nomme par raccourci l’usine d’Orléans, dont elle est située à quelques encablures) fabrique des tables de cuisson à induction ainsi que des fours d’encastrement standard, tandis que l’usine de Vendôme produit des fours micro-ondes ou de petit volume ainsi que des tables de cuisson à induction de petit et grand formats et des tables gaz.
Le site d’Orléans s’étend sur 38 000 m2. Il a une capacité de production de 500 000 pièces par an. Actuellement, 500 tables de cuisson et 800 fours y sont fabriqués chaque jour. Mais Frédéric Guerel nous explique que selon les besoins, le rythme peut être adapté. Par exemple, les équipes qui travaillent en 2/8 peuvent travailler en 3/8 si besoin.
Cette capacité d’adaptation est liée à l'organisation mais aussi à l’expertise des opérateurs. Par exemple, sur les lignes de production de fours, qui comptent chacune 16 à 18 personnes, ces dernières sont capables de fabriquer tous les types de fours ; il est donc possible de passer facilement de l'assemblage d'un modèle à un autre. En outre, dès les premiers mètres que nous parcourons dans l’usine, nous découvrons que l'outillage est entretenu et réparé sur place ; les machines sont aussi modifiées pour les adapter aux besoins de fabrication.
Des matières premières au produit fini, fabriquer en France pour préserver un savoir-faire
Produire en France, dans cette usine historique, est aussi une manière de préserver un « savoir-faire » et d’exiger une forme « d’excellence », des mots souvent cités par nos interlocuteurs lors de cette visite.
Ce savoir-faire commence avec la fabrication des pièces de base. À Orléans, on ne se contente pas d’assembler, loin de là. Toutes les étapes sont effectuées sur place, depuis le façonnage des matières premières jusqu’à l’assemblage puis l’emballage des produits finis, comme en témoignent les énormes bobines d’acier qu’on croise en chemin, mais aussi de l’inox, du cuivre ou encore de l’alu. Toute la journée, les presses produisent des pièces de différents types (qui alimentent les deux usines, d’Orléans et de Vendôme, la plupart étant fabriquées ici). Le site d'Orléans utilise pas moins de 40 tonnes d’acier par jour et 600 à 700 kg de cuivre.
L'entreprise applique la même logique de proximité au choix des matières premières et composants, qui proviennent au maximum de France, à l’instar de l’acier fourni en majorité par ArcelorMittal. Là encore, la position centrale des usines dans l’Hexagone est un avantage pour l’acheminement des matières premières.
Le groupe fabrique les cavités de ses fours, les pièces qui constituent fours et tables de cuisson, mais surtout, ses propres inducteurs – d’où la consommation importante de cuivre. 100% des inducteurs équipant les tables de cuisson des trois marques Brandt, Sauter et De Dietrich sont fabriqués à Orléans. Cela représente environ 4000 plateaux inducteurs par jour. Ces gestes, réalisés en partie par des machines mais nécessitant aussi un certain nombre de manipulations manuelles, constituent un vrai savoir-faire. C’est notamment le cas du travail de bobinage, très spécifique. Fabriquer ses propres inducteurs dans ses usines permet une véritable maîtrise de la qualité mais aussi en matière de puissance nous explique-t-on.
Asseoir l’activité du site sur l’humain
Lors de cette visite, nous avons été surpris de l’omniprésence des interventions humaines, contrairement à certaines usines bien plus automatisées. Que ce soit pour les fours ou les tables de cuisson, beaucoup d’étapes restent manuelles. Interrogé sur ce point, Frédéric Guerel évoque de futurs investissements dans des lignes semi-automatisées, admettant qu’elles sont actuellement « très peu automatisées ». Même si le but n’est pas du tout de remplacer l’humain, au contraire.
« On bâtit autour de l’humain » assène-t-il, expliquant par exemple que Brandt a mis en place un « dojo ». Il s’agit d’un centre d’apprentissage où les employés bénéficient régulièrement de formations sur la qualité, la sécurité… Les récents investissements consentis par l'entreprise reflètent parfaitement cette volonté du Groupe Brandt de trouver un équilibre entre automatisation et savoir-faire manuel. Par exemple, des sommes conséquentes ont été allouées à l’amélioration de l’ergonomie des lignes. Certains investissements récents concernent aussi des équipements qui assistent les opérateurs dans leurs missions pour atteindre une qualité optimale. Par exemple, le site s’est doté l’année dernière d’une machine pour guider l’opérateur à chaque étape de l’assemblage du bandeau et des manettes des fours. Il s’agit d’une assistance par informatique, où chaque opération est validée.
Du côté des tables de cuisson, l’usine a investi dans une nouvelle machine très coûteuse pour réaliser le collage des commandes sur la table le plus précisément possible. Là encore, il s’agit d’une assistance puisqu’un opérateur reste aux commandes. L’emplacement des composants, notamment de la carte électronique, est calculé au centième de millimètre près. Le groupe possède deux machines de ce type, une à Orléans, l’autre à Vendôme.
Dans un souci de qualité, des contrôles sont effectués à diverses étapes. Chaque produit sans exception subit un contrôle sur les critères de la sécurité, des performances et de l'esthétique ; Brandt parle de « contrôle à 100% ». En plus de ces vérifications systématiques, 1% de la production est prélevée pour réaliser des tests en profondeur. Ils s’ajoutent à des tests déjà effectués en amont dans les laboratoires, pendant la phase de développement, par des chefs cuisiniers et techniciens.